Batching
The concrete was produced using the
concrete mixing station at the DTI laboratories. The main challenge
of the concrete production was to comply with the requirement of
less than 1% batching deviation on the individual constituent. In
particular the water content was a challenge and a special
procedure for controlling aggregate moisture content was
established.
In connection with the production
of each batch of concrete the moisture content in the individual
aggregate fraction was determined by micro wave drying on three
samples of approximate 1 kg each taken directly from the material
actually batched, i.e. from the material on the conveyor belt. The
adopted procedure also allowed to batch exactly the nominal amount
of aggregate as material could be added or removed from the
conveyor belt to equal precisely the desired amount. The total time
required to obtain the moisture content of four aggregate fractions
was approximately 25 minutes. During this time the aggregate was
resting in the closed confines of the mixer, i.e. no moisture loss
took place. From the measured moisture contents the exact amount of
water needed to obtain the w/c-ratio was calculated and
subsequently batched.
The maximum deviation on the
w/c-ratio was 0.86 % corresponding to values between 0.397 - 0.403
for a nominal value of 0.400, i.e. roughly 10 times better than
what is typically achieved by industrial concrete mixing
stations.
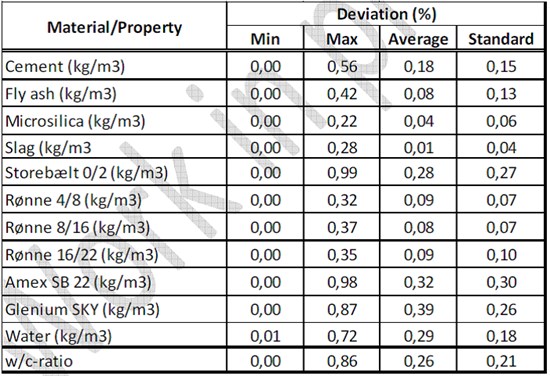
Based on the data for the +60
batches of concrete produced, the minimum, maximum, average and
standard deviations obtained for the individual
constituent.
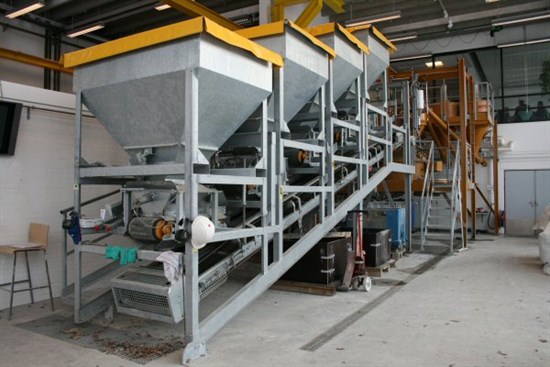
The mixing station is equipped
with a 375/250 liter counter-current mixer, five aggregate silos
and four powder silos from Haarup A/S, and process control software
from Skako A/S. Prior to initiation of the project all weight cells
were calibrated using traceable weights. All materials were batched
based on weight.